Texte : Pierre-Antoine Preti
Construire un grand bateau composite tient du savoir-faire culinaire. Rencontre à Ecublens, quelques heures après le départ de BoatOne pour Barcelone. Un moment rempli d’émotion pour Jean-Marie Fragnière, le responsable de la construction. Le chef de cette cuisine trois étoiles revient sur l’aventure technique, partagée avec une équipe extraordinaire de 30 boat builders.
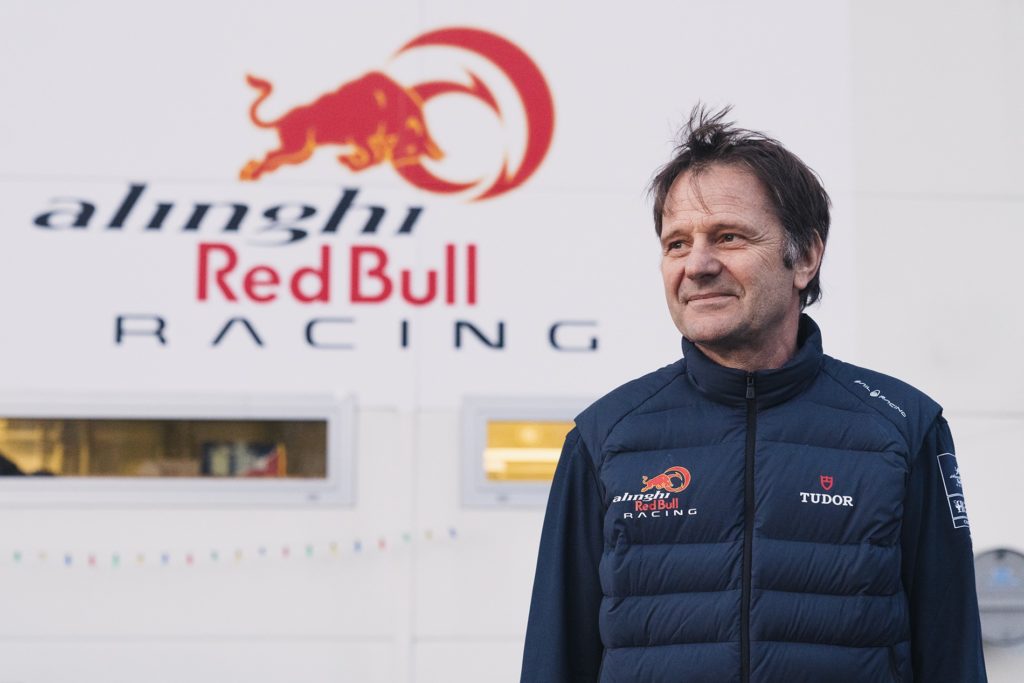
C’est un jeudi après-midi, au début du mois de mars. Dans la grisaille de cette fin d’hiver, le chantier historique de Décision SA a un petit air de fête. Trois jours plus tôt, l’immense coque de BoatOne, l’unique AC75 construit par Alinghi Red Bull Racing, s’en allait rejoindre BoatZéro dans la base de Barcelone. Sur les hauts d’Ecublens, quelques-uns des 30 boat builders embarqués dans l’aventure prennent leur pause sur la terrasse. Désormais propriété de l’équipe suisse, l’ancien chantier Décision SA n’a plus aucun secret pour Jean-Marie Fragnière, qui a tout vécu ici depuis les années 90 : des multicoques lémaniques à Solar Impulse, en passant par les Alinghi de l’America’s Cup. Le responsable de la construction avait quitté l’entreprise en 2017, pour s’occuper de la mise en place technique des TF35. À peine ce job terminé, Jean-Marie a reçu un nouveau coup de fil. Une mission qui ne se refuse pas. Il a rembrayé pour deux ans.
Une construction itérative
Démarrée au printemps dernier, la démarche de construction est forcément itérative. Le plan total du bateau n’est pas terminé au moment où elle démarre. Les allers et retours entre constructeurs, ingénieurs et architectes sont permanents. « À un moment donné, il faut quand même geler les plans pour démarrer la construction des machines. » La coque est d’abord mise en œuvre, puis le pont. Les structures intérieures sont ajoutées, avant de fermer le pont. C’est ensuite à la lampe frontale que toutes les parties sont soudées, « greffées », comme on dit dans le jargon.
Le Deed of Gift de l’America’s Cup exige que le bateau doit être « constructed in the country ». Pour la 37e édition, la jauge est bien plus restrictive qu’une simple « box rule ». Les matériaux sont jaugés. Le poids minimum des nids d’abeilles, la rigidité des fibres, le poids du bateau, tout est régenté par la jauge du Defender kiwi. « Nous travaillons aujourd’hui avec les mêmes matériaux qu’en 2003, mais c’est leur mise en œuvre qui a beaucoup évolué. La jauge permet le contrôle des coûts tout en limitant la recherche et le développement. En revanche, les nombreux points de mesure imposés dans la structure impliquent des contrôles réguliers tout au long de la fabrication. »
Dix nationalités sur le chantier
Comme toujours en matière d’America’s Cup, le projet est pharaonique sur le plan des ressources humaines. Il est bien au-delà des pratiques habituelles dans notre pays. L’équipe compte dix nationalités, dont une moitié suisse. Pour les encadrer, les teamleaders Simon Bovay, David Nikles et Danny Cawsey ont apporté leurs sciences de la construction navale. Il y avait aussi deux ingénieurs (un pour le suivi qualité et l’autre pour les échanges avec le design team barcelonais), une personne pour la commande numérique à plein-temps, un spécialiste de la découpe des matériaux et un responsable RH qui s’occupe entre autres du bien-être de l’équipe. À cela s’ajoutent les collaborations temporaires d’autres constructeurs privés.
Comme lors des éditions précédentes, l’EPFL est de la partie. Le laboratoire de mise en œuvre de composites à haute performance (LPAC) de la professeure Véronique Michaud a aidé à valider et caractériser les matériaux.
Un chantier ancré dans le tissu économique suisse
Au niveau helvétique, une trentaine de PME ont collaboré. Certaines ont fabriqué des moules. Il y a eu notamment des ateliers de mécanique, des serruriers, des transporteurs, des transitaires pour les paperasses douanières…
Pour Jean-Marie Fragnière, une des clés de ce type d’entreprise réside dans la bonne tenue du planning. « Tout le travail se base sur la date de livraison du bateau, connue depuis deux ans. Nous devons nous adapter à cette contrainte. Nos délais ne sont pas extensibles.»
Or certains matériaux demandent huit mois d’attente à la livraison. Il serait donc fatal de sous-estimer la commande. Sébastien Schmidt est le project manager qui s’occupe du planning. Il doit acquérir toutes les fournitures nécessaires à temps. La coordination des commandes et des actions à réaliser est un des aspects les plus importants de cette cuisine composite. C’est la bible des boat builders.
La cuisson, un moment risqué
La cuisson est un moment extrêmement risqué. Sa réussite dépend de la qualité du vide créé dans l’étuve, de son étanchéité. Chaque pièce demande entre trois et cinq passages dans le four. Ce qui est relativement simple pour les petites étuves ne l’est pas forcément pour les plus grosses. À Ecublens, le grand four a un volume suffisamment grand pour cuire l’AC75 en entier. Certaines cuissons peuvent durer jusqu’à 16 heures. Il faut surveiller l’homo- généité de la cuisson. L’opération ne peut pas être interrompue. Il faut une fourniture électrique stable et régulière pendant toute la durée de l’opération. « Or, l’hiver dernier, il était question de contingentement et de pénuries d’électricité. Nous avons loué une grosse génératrice au cas où. Heureusement, nous n’avons pas eu besoin de l’utiliser. »
Après chaque cuisson, il y a l’émotion du démoulage. Il y a aussi l’anxiété de la vérification. Sur ce chantier, toutes les parties du bateau ont été systématiquement contrôlées par échographie. L’ennemi, ici, c’est la porosité des matériaux et le délaminage des tissus. Rien n’a été laissé au hasard.
Un convoi exceptionnel
Le 28 février dernier, la coque est partie en convoi exceptionnel vers Barcelone. Sous bonne escorte, BoatOne a voyagé pendant plusieurs jours. C’est une aventure en soi. Avec ses cinq mètres de large, des arbres mal taillés sur des routes nationales ou des mobiliers urbains peuvent parfois bloquer le passage.
À Ecublens, le soir du départ, il a fallu démonter un panneau de circulation sur le premier giratoire, à un jet de cailloux du chantier.
Mais la livraison de l’AC75 ne signifie pas l’arrêt du travail en Suisse. Le chantier continue la fabrication de pièces. Il est aussi en stand-by, au cas où. Les teamleaders et une partie des constructeurs vont s’installer à Barcelone. La base suisse est bien acha- landée. Les moules de la coque restent à Ecublens. En cas d’avarie majeure, les deux chantiers travail- leront de concert.
Pour Jean-Marie Fragnière, le boulot est donc loin d’être terminé. Mais la tête du responsable de la construction est déjà pleine de souvenirs. Le plus beau d’entre eux restera probablement le premier assemblage complet de la coque du bateau. Un grand moment d’émotion ! « Je suis très fier de cette équipe. Les boat builders ont été très solidaires entre eux. Je sais qu’avec l’America’s Cup, il est difficile de prévoir l’avenir, mais j’espère que l’on pourra retravailler avec ce collectif une autre fois… »
Mais ça, c’est déjà une autre histoire ! Avec la livraison de la coque, les boat builders ont passé le témoin aux marins. BoatOne est désormais installé à Barcelone. Si son aventure technique continue, le cahier des charges s’annonce résolument sportif.